3-Axis vs. 5-Axis CNC Machines: Which is Right for Your Needs?
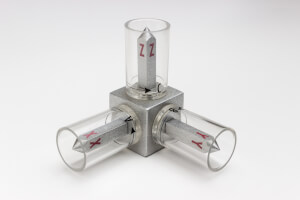
3-Axis vs. 5-Axis CNC Machines: Which is Right for Your Needs?
CNC (Computer Numerical Control) machining is a vital process in modern manufacturing, allowing for the precise and efficient creation of complex parts and components. Among the various types of CNC machines, 3-axis and 5-axis machines are the most commonly used. But how do they differ, and which one is better for your specific needs? This article will explore the differences between 3-axis and 5-axis CNC machines, including their features, benefits, and the industries that use them.
What is a 5-Axis CNC Machine?
A 5-axis CNC machine is a sophisticated piece of equipment capable of moving a tool or a part across five different axes simultaneously. This capability allows for the creation of intricate and highly precise parts with fewer setups and greater efficiency.
Features of a 5-Axis CNC Machine
- Simultaneous Movement: The machine can move the tool along the X, Y, and Z linear axes and rotate it along the A and B axes.
- Complex Geometries: Capable of machining complex shapes and contours that would be difficult or impossible with a 3-axis machine.
- Reduced Setups: Allows for machining multiple faces of a part in a single setup, reducing the need for repositioning.
Understanding Each Axis and How It Works
- X-Axis: Moves the tool left and right.
- Y-Axis: Moves the tool forward and backward.
- Z-Axis: Moves the tool up and down.
- A-Axis: Rotates around the X-axis, allowing the tool to tilt.
- B-Axis: Rotates around the Y-axis, enabling the tool to pivot.
Core Benefits of 5-Axis CNC Machining
- Greater Precision: The ability to machine complex shapes with fewer setups reduces the risk of errors and improves overall accuracy.
- Enhanced Surface Finish: The tool can maintain a consistent orientation relative to the surface, leading to smoother finishes.
- Reduced Lead Times: By machining parts in fewer setups, 5-axis machines can significantly reduce production times.
- Versatility: Suitable for a wide range of materials, including metals, plastics, and composites.
Industries That Use 5-Axis CNC Machining
- Aerospace: For producing complex components such as turbine blades and aircraft parts.
- Automotive: Used in the production of high-performance engine components and prototypes.
- Medical: For creating intricate surgical instruments and implants.
- Energy: In the machining of components for wind turbines, oil, and gas equipment.
What is 3-Axis CNC Machining?
A 3-axis CNC machine is the most basic type of CNC machine, moving the tool or part along three primary axes: X, Y, and Z. This type of machining is commonly used for simple and flat geometries.
Understanding Each Axis and How It Works
- X-Axis: Moves the tool left and right.
- Y-Axis: Moves the tool forward and backward.
- Z-Axis: Moves the tool up and down.
Core Benefits and Limitations vs. 5-Axis CNC Machining
Benefits:
- Simplicity: Easier to program and operate, making it ideal for straightforward tasks and beginners.
- Cost-Effective: Generally less expensive to purchase and maintain than 5-axis machines.
- Suitable for Simple Geometries: Works well for parts with simple shapes and flat surfaces.
Limitations:
- Limited Complexity: Unable to machine complex shapes and undercuts without multiple setups.
- More Setups Required: Often requires repositioning the part multiple times to achieve the desired shape, increasing the risk of errors.
- Longer Lead Times: More setups and repositioning can extend production times compared to 5-axis machining.
Industries That Use 3-Axis vs. 5-Axis CNC Machining
3-Axis CNC Machining: Commonly used in industries like automotive, construction, and furniture manufacturing for producing simple parts and components.
5-Axis CNC Machining: Preferred in industries requiring high precision and complex geometries, such as aerospace, automotive, medical, and energy.
Finding the Right Machine for Your Needs
Choosing between a 3-axis and a 5-axis CNC machine depends on several factors:
- Complexity of Parts: If you need to produce complex parts with intricate geometries, a 5-axis machine is likely the better choice.
- Production Volume: For high-volume production of simple parts, a 3-axis machine may be more cost-effective.
- Budget: Consider your budget for purchasing and maintaining the machine. While 5-axis machines offer more capabilities, they are also more expensive.
How Much Harder is it to Program a 5-Axis vs. a 3-Axis Machine?
Programming a 5-axis CNC machine is generally more complex than programming a 3-axis machine. The additional axes introduce more variables, requiring a deeper understanding of CNC programming and more advanced software. However, modern CAM (Computer-Aided Manufacturing) software has made it easier to program 5-axis machines, providing tools and simulations to help operators create efficient and accurate tool paths.
How Does 5-Axis Shorten Cycle Times and Improve Quality Control?
Shortened Cycle Times
- Fewer Setups: The ability to machine multiple faces of a part in a single setup reduces the time spent repositioning the part.
- Simultaneous Machining: The capability to move along five axes simultaneously allows for more efficient cutting paths, reducing overall machining time.
Improved Quality Control
- Consistent Tool Orientation: Maintaining a consistent tool orientation relative to the part surface reduces the risk of tool marks and imperfections.
- Reduced Handling: Fewer setups mean less handling of the part, which reduces the risk of errors and ensures higher quality consistency across production runs.
Conclusion
Both 3-axis and 5-axis CNC machines have their place in modern manufacturing, offering unique advantages depending on the application. While 3-axis machines are ideal for simpler tasks and offer cost savings, 5-axis machines excel in producing complex parts with greater precision and efficiency. Understanding your specific needs and the demands of your industry will help you choose the right CNC machine for your operations. Whether you opt for the simplicity of a 3-axis machine or the advanced capabilities of a 5-axis machine, both technologies are essential tools in the world of precision manufacturing.