A Detailed Guide to CAD: History, Usage, and the Future
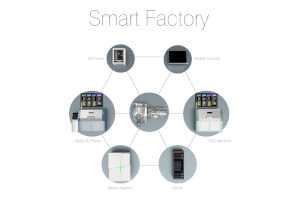
CAD
Computer-Aided Design (CAD) is a technology that has revolutionized the way we design and manufacture products. CAD software enables engineers, architects, and designers to create precise digital models of objects, ranging from simple parts to complex assemblies. These models can be used to visualize, simulate, and refine designs before they are manufactured, reducing errors and costs associated with physical prototyping.
A Detailed History and Overview of CAD
The concept of CAD dates back to the 1960s, during the early days of computer technology. Dr. Patrick J. Hanratty, often considered the 'father of CAD,' developed the first numerical control system that led to the development of CAD software. His work laid the foundation for the integration of computers in design and manufacturing.
The first true CAD software, Sketchpad, was developed by Ivan Sutherland in 1963 as part of his Ph.D. thesis at MIT. Sketchpad introduced many concepts that are still fundamental in modern CAD software, such as the use of a graphical user interface and the ability to manipulate graphical objects interactively.
Throughout the 1970s and 1980s, CAD technology evolved rapidly, with the introduction of more powerful computers and software. Companies like Autodesk, founded in 1982, played a significant role in bringing CAD to the masses with the release of AutoCAD, one of the first widely adopted CAD programs. By the 1990s, CAD had become an essential tool in industries such as automotive, aerospace, architecture, and consumer products.
How CAD Modeling Works with CNC Machines
CAD modeling is closely linked with CNC (Computer Numerical Control) machining. In a typical workflow, a designer creates a 3D model of a part using CAD software. This model is then translated into a series of instructions (G-code) that CNC machines use to precisely cut, shape, or form the part from raw material.
Here’s how CAD integrates with CNC machining:
- Design Phase: The process begins with the creation of a detailed 3D model in CAD software. The model defines the geometry, dimensions, and features of the part.
- Simulation and Testing: CAD software allows for simulation of the machining process, where potential issues like tool collisions or material wastage can be identified and corrected before actual machining begins.
- CAM Integration: The CAD model is then imported into CAM (Computer-Aided Manufacturing) software, which generates the tool paths and G-code needed for CNC machining.
- Machining: The G-code is uploaded to a CNC machine, which executes the instructions to produce the physical part. This integration ensures high precision and repeatability in manufacturing.
Historical Timeline of CAD Development
- 1963: Ivan Sutherland develops Sketchpad, the first interactive CAD program.
- 1971: Dr. Patrick J. Hanratty develops ADAM (Automated Drafting and Machining), an early CAD/CAM system.
- 1982: Autodesk releases AutoCAD, making CAD technology widely accessible.
- 1987: Pro/ENGINEER (later PTC Creo) introduces parametric modeling, allowing more intuitive and flexible design changes.
- 1995: SolidWorks launches its CAD software, bringing 3D solid modeling to a broader audience.
- 2000s: The rise of cloud-based CAD platforms, such as Onshape, allows for collaborative design and easier access.
- 2010s: CAD software begins to integrate more advanced simulation, generative design, and AI-driven features.
The Top 10 Most Used CAD CAM Software
- AutoCAD: Widely used for 2D drafting and 3D design, especially in architecture and civil engineering.
- SolidWorks: Popular in mechanical design and engineering for its robust 3D modeling and simulation tools.
- PTC Creo: Known for parametric and direct modeling, used in complex product design and manufacturing.
- CATIA: Developed by Dassault Systèmes, CATIA is used in aerospace and automotive industries for advanced modeling and simulation.
- Siemens NX: An integrated CAD/CAM/CAE system used in high-end engineering, especially in aerospace and automotive sectors.
- Fusion 360: A cloud-based CAD/CAM/CAE tool that offers a complete product development process, from design to manufacturing.
- Onshape: A cloud-based CAD platform that allows for real-time collaboration and design sharing.
- Rhino: Known for its flexibility in modeling complex surfaces and curves, widely used in industrial design and architecture.
- Autodesk Inventor: A mechanical design tool offering parametric modeling, simulation, and automated product configuration.
- Mastercam: A leading CAM software that integrates with various CAD systems for toolpath generation and CNC programming.
Pros and Cons of CAD
Pros
- Precision: CAD allows for the creation of highly accurate and detailed designs, reducing errors in manufacturing.
- Efficiency: CAD significantly speeds up the design process, enabling quicker iterations and refinements.
- Visualization: Designers can visualize and simulate their designs, allowing for better decision-making and problem-solving.
- Collaboration: Modern CAD platforms facilitate collaboration among teams, even when they are geographically dispersed.
- Cost-Effective: By reducing the need for physical prototypes, CAD can lower the overall cost of product development.
Cons
- Learning Curve: CAD software can be complex and requires significant training to master.
- Cost: High-end CAD software can be expensive, both in terms of licensing and required hardware.
- Dependence on Technology: CAD systems require powerful computers and consistent maintenance, making them reliant on technological infrastructure.
Cost and Usage of CAD Software
The cost of CAD software varies widely depending on the complexity of the tool, the licensing model, and the specific industry it serves:
- Subscription Models: Many CAD software providers now offer subscription-based pricing, making it more affordable for small businesses and startups.
- One-Time Purchase: Some CAD tools still offer perpetual licenses, though these often come with higher upfront costs.
- Free and Open Source: There are free CAD tools available, such as FreeCAD, though they may lack the advanced features of commercial software.
Usage of CAD software spans multiple industries, including:
- Manufacturing
- Automotive
- Aerospace
- Architecture
- Consumer Products
- Electronics
- Medical Devices
The Present and Future of CAD
Present
Today, CAD software is more powerful and accessible than ever. Cloud-based platforms have revolutionized collaboration, allowing teams to work together in real-time from anywhere in the world. The integration of CAD with CAM and CAE (Computer-Aided Engineering) tools has streamlined the entire product development process.
Future
The future of CAD is likely to be shaped by several emerging technologies:
- AI Integration: Artificial intelligence is beginning to play a role in CAD, with features like generative design that can automatically optimize designs based on specified parameters.
- Virtual and Augmented Reality: VR and AR technologies will allow designers to immerse themselves in their models, enabling a more intuitive design process.
- Increased Automation: The automation of repetitive tasks will further reduce the time required for design iterations and modifications.
- Sustainability: As environmental concerns grow, CAD tools will increasingly focus on sustainability, helping designers create eco-friendly products with minimal waste.
What Does CAD Look Like with AI?
Artificial Intelligence is set to transform CAD in significant ways:
- Generative Design: AI can analyze design constraints and automatically generate optimized designs, saving time and improving performance.
- Predictive Analysis: AI-driven tools can predict how designs will perform under various conditions, allowing for more informed decision-making early in the design process.
- Customization: AI will enable more personalized design processes, tailoring tools and features to the specific needs of the user.
- Error Reduction: AI can identify potential design flaws and suggest corrections before they become costly mistakes in production.
Conclusion
CAD has come a long way since its inception in the 1960s, evolving into an indispensable tool across industries. As technology advances, the integration of AI, cloud computing, and other innovations will continue to expand the capabilities of CAD, making it more powerful, intuitive, and accessible. Whether you’re a seasoned engineer or a budding designer, understanding the history, present, and future of CAD will help you leverage its full potential in your work.