Understanding Surface Grinders: Essential Tools for Precision Surface Grinding
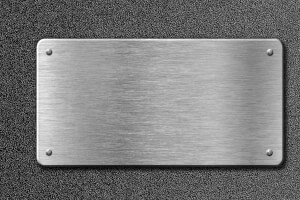
Understanding Surface Grinders: Essential Tools for Precision Surface Grinding
Surface grinders are indispensable machines in the manufacturing and machining industries, known for their ability to produce flat surfaces with high precision. These machines play a critical role in various applications, including tool and die making, mold manufacturing, and parts production. In this article, we will explore the functionality of surface grinders, the surface grinding process, and highlight some top brands, including Okamoto and Chevalier.
What is Surface Grinding?
Surface grinding is a machining process that utilizes a rotating abrasive wheel to remove material from a workpiece, creating a flat and smooth surface. The primary objective of surface grinding is to achieve a desired finish while maintaining tight tolerances.
Key Features of Surface Grinding
- Precision: Surface grinders are capable of achieving fine tolerances, making them ideal for applications requiring high precision.
- Versatility: These machines can grind various materials, including metals, plastics, and composites.
- Efficiency: Surface grinding is a fast and efficient process, suitable for both small-scale and large-scale production.
How Surface Grinders Work
The operation of a surface grinder involves several key components:
- Abrasive Wheel: The main tool used for grinding, the abrasive wheel is made up of hard particles bonded together. The choice of wheel depends on the material being ground and the desired finish.
- Table: The workpiece is mounted on a table that moves horizontally (and sometimes vertically) to facilitate the grinding process. The table can be manually operated or automated, depending on the machine's design.
- Cross Feed: This feature allows the grinding wheel to move across the workpiece, effectively removing material.
- Coolant System: Many surface grinders come equipped with a coolant system to reduce heat generated during the grinding process, extending tool life and improving surface finish.
The Surface Grinding Process
- Setup: The workpiece is securely mounted on the grinder's table.
- Grinding: The abrasive wheel rotates at high speeds while the table moves the workpiece under the wheel. The grinding action removes material, creating a smooth surface.
- Finishing: After the initial grinding, finer wheels may be used for finishing passes to achieve the desired surface quality.
Top Brands in Surface Grinding
When it comes to surface grinders, several brands are recognized for their quality, precision, and reliability. Here are two of the top brands:
Okamoto Surface Grinders
Okamoto is a leading manufacturer of surface grinding machines known for their advanced technology and precision engineering. Their surface grinders are designed for high-performance applications, offering features such as:
- Automatic Grinding Cycle: Okamoto surface grinders often come with programmable controls that allow for automatic grinding cycles, enhancing efficiency.
- High Rigidity: The construction of Okamoto grinders ensures stability during operation, leading to improved surface finish and accuracy.
- Diverse Models: Okamoto offers a wide range of surface grinders, from manual to fully automatic, catering to various industry needs.
Chevalier Surface Grinders
Chevalier is another prominent name in the surface grinding industry, recognized for its innovative designs and user-friendly machines. Key features of Chevalier surface grinders include:
- Robust Design: Chevalier grinders are built with solid construction to ensure long-lasting performance and precision.
- Easy Operation: Many Chevalier models are equipped with intuitive controls, making them accessible for operators of all skill levels.
- Versatility: Chevalier offers different types of surface grinders, including flat and rotary models, suitable for various applications.
Applications of Surface Grinders
Surface grinders are used across a wide range of industries due to their versatility. Some common applications include:
- Tool and Die Making: Creating precision tools and dies for manufacturing processes.
- Mold Manufacturing: Producing molds for plastic injection and casting.
- Automotive Components: Grinding surfaces of engine components, shafts, and other precision parts.
- Aerospace Parts: Ensuring high precision in components used in aircraft and spacecraft.
Conclusion
Surface grinders play a vital role in achieving precision finishes and tolerances in various machining applications. With the ability to grind different materials and produce flat surfaces with high accuracy, they are essential tools in the manufacturing sector.
Brands like Okamoto and Chevalier have established themselves as leaders in the surface grinding market, offering reliable machines equipped with advanced features. As industries continue to demand higher precision and efficiency, surface grinders will remain an indispensable part of the machining process.
Whether you're in tool making, mold manufacturing, or any field that requires high-quality surface finishes, investing in a quality surface grinder is key to achieving your production goals.